Automotive
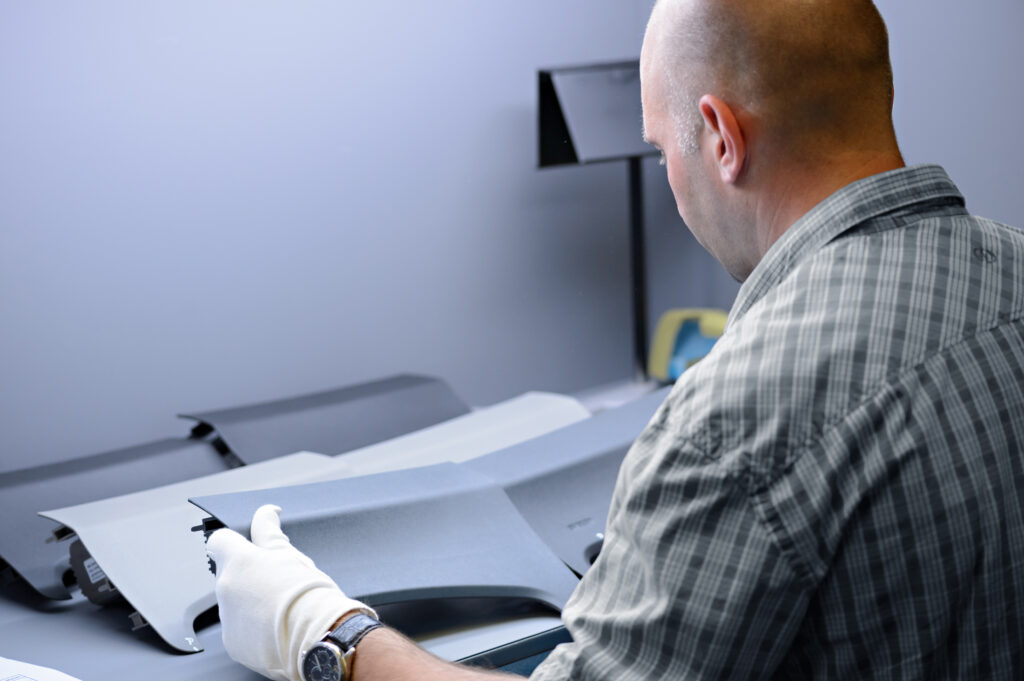
Analytik-Dienstleistungen für Automobilzulieferer
Komplettlösungen von Freigabeprüfung über Umweltsimulation bis Schadenanalytik
Speziell für die Automobilzulieferer der Bereiche Kunststoffe, Lacke und Beschichtungen, sowie Chemiefasern und Textilien gibt es separate Seiten mit typischen Fragestellungen zu diesen Schwerpunkten. Daneben untersuchen wir auch andere Materialien wie Glasoberflächen, Reibbeläge, elektronische Bauteile wie Schalter und Platinen und vieles mehr.
Im Rahmen der Erstmusterprüfungen Automobil wird von unserer Rohstoff- und Produktanalytik eine Identifikationsprüfung und Spezifikationsprüfung gemäß Ihrer OEM-Vorschriften durchgeführt. Entsprechend testen wir auch die Beständigkeit Ihrer Proben während verschiedener Umweltsimulationsprüfungen. Wir erstellen gerne Ihr individuelles Analysenpaket.
Auch den Aufbau von Wettbewerbsprodukten können wir für Sie analysieren. Gerade dann, wenn es schwierig wird, nämlich bei der Aufklärung von Schadensfällen oder bei Reklamationen, hilft Ihnen unsere Schadensfallanalytik weiter. Hierbei stehen wir Ihnen gerne als unabhängiger Berater zur Verfügung und liefern Ihnen professionell ausgearbeitete Prüfberichte, die sie direkt an Ihre Zulieferer weiterleiten können. Sollte eine Reklamation auf Prozessprobleme hindeuten oder sollten Sie eine Prozessoptimierung planen, so unterstützen wir Sie gerne.
Die in der Automobilindustrie gängige IATF 16949 fordert für Analysen eine Beauftragung von nach ISO 17025 akkreditierten Prüflaboratorien. Diese Bedingung erfüllen wir seit vielen Jahren. Wir bieten Ihnen einen umfassenden und schnellen analytischen Service aus einer Hand.
Weitere Informationen

